Hyundai and Kia are working to develop cheaper cathode materials for lithium iron phosphate (LFP) batteries. That way they can reduce their reliance on Chinese battery suppliers.
The idea is to develop a new production process for LFP cathode material, according to the pair. Instead of adding lithium to phosphate and iron sulphate precursors, a new process would combine iron powder, phosphate, and lithium without a precursor step.
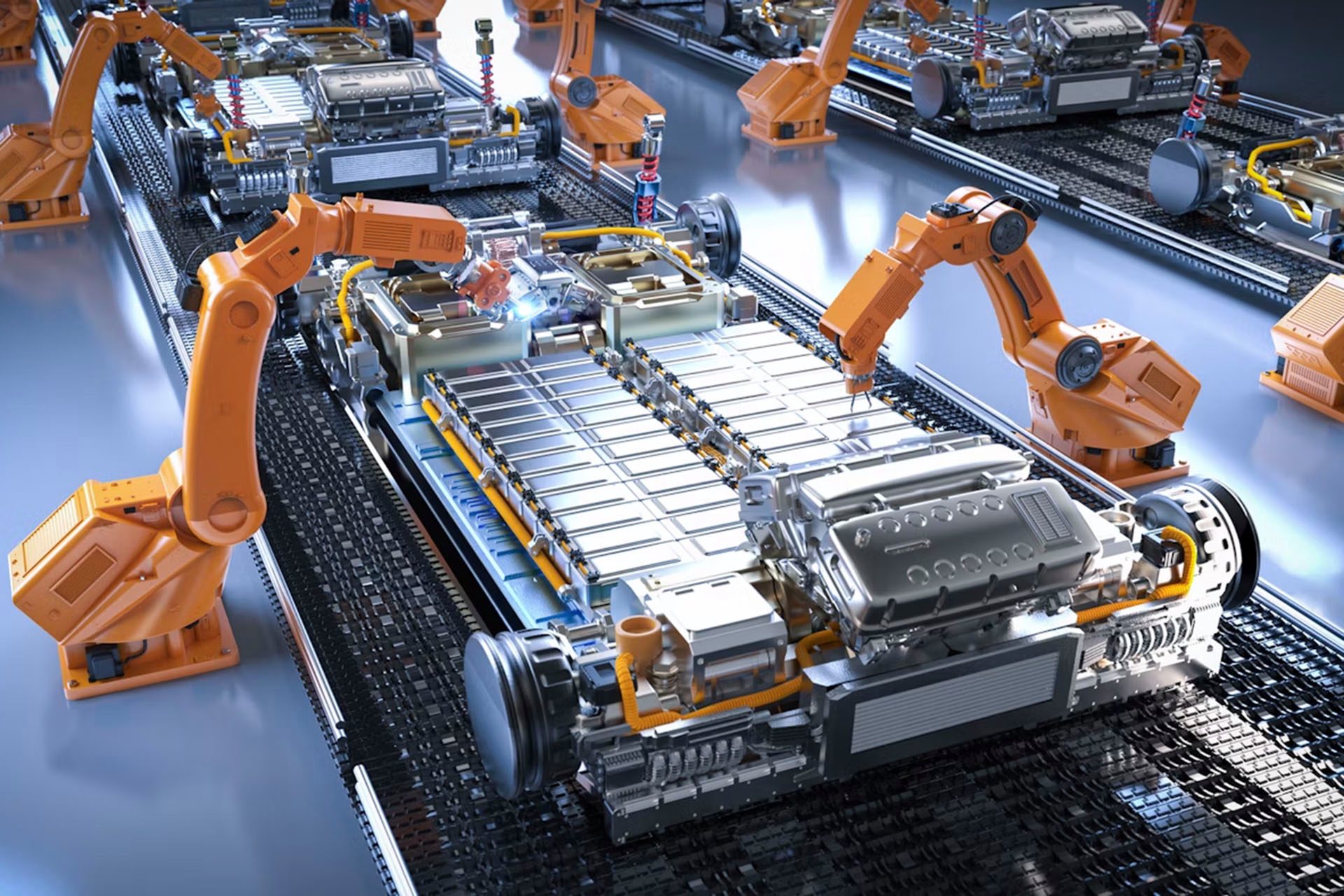
By sidestepping this process the pair hope to cut costs and minimise the environmental impact of the battery-production process. It will also lay the foundation for greater LFP battery cell manufacturing in Korea.
This release comes roughly 12 months after Hyundai said it was initiating a two-year joint venture to develop LFP batteries in South Korea. The reason is that it reduces its dependence on Chinese battery suppliers while also making LFP cells more affordable.
LFP technology originated in the U.S. but was soon abandoned as it was deemed unprofitable. However, several Chinese companies proved otherwise. Now LFP tech is used in the base Tesla Model 3 and Ford Mustang Mach-E.
Around 20 per cent of the world’s batteries for electric vehicles use LFP chemistry. It doesn’t require nickel or cobalt, and is less prone to overheating, thermal runaway, and heat-related degradation.
China’s BYD and CATL are the world’s largest makers of LFP batteries. Ford plans to make LFP batteries in Michigan, but the cells will come from a Ford-owned factory using Chinese production methods. GM is also moving to LFP cells for its next-generation Chevrolet Bolt EV, due in 2025.
Meantime, China continues to innovate on the LFP battery chemistry. GAC has introduced LFP cells with a 20 per cent boost in energy density, while CATL claims next-gen LFP cells can add 400km of range in 10min.