Volvo is set to do a Tesla and introduce mega-casting for its next-generation electric cars. The firm says it will improve efficiency and create more freedom for future vehicle design.
The new system is set for introduction in 2025/6, likely for the upcoming EX60 which will be produced in Sweden.
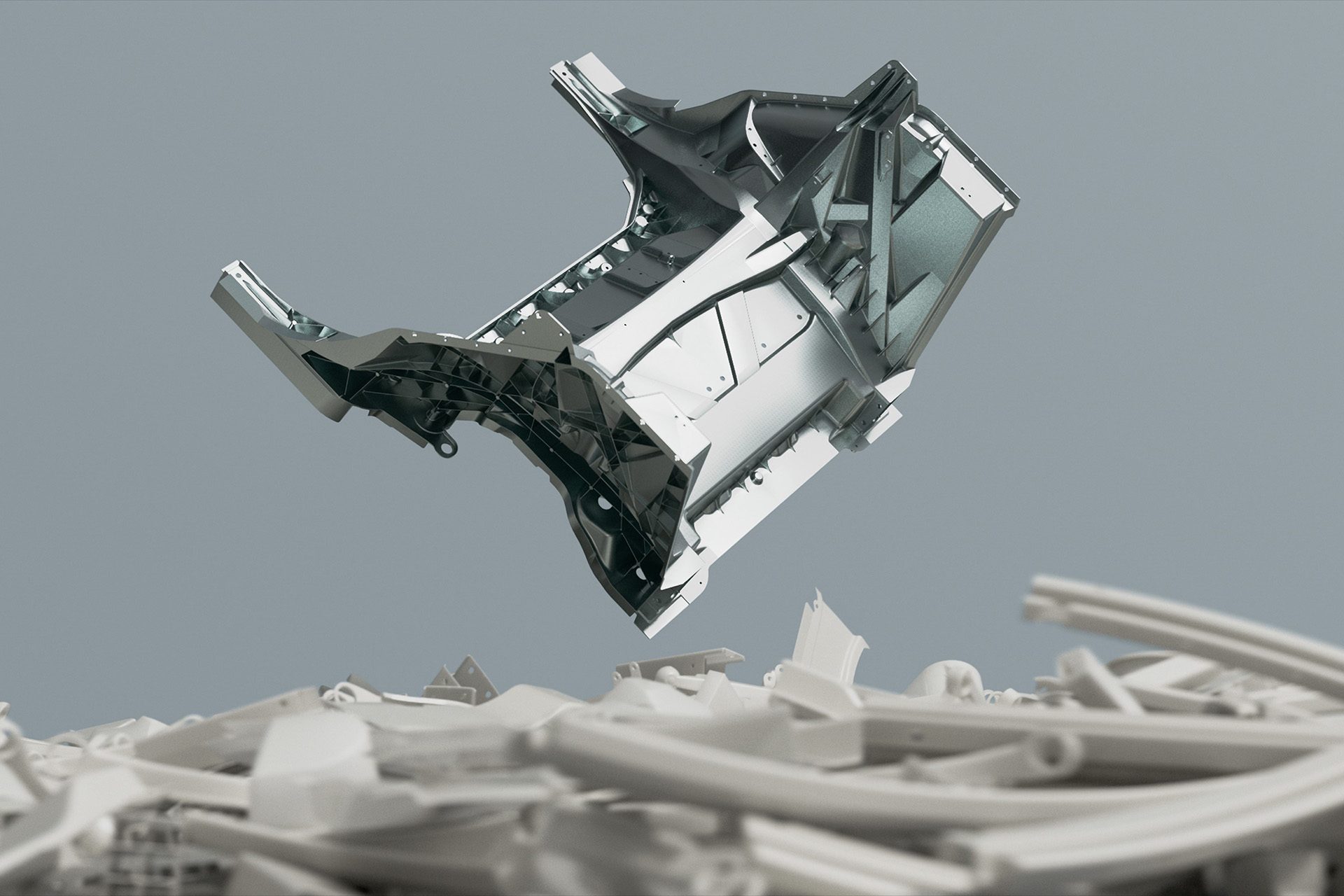
Evidently the process is linked with the introduction of the SPA3 platform, the third iteration of the existing electric platform.
Volvo has not said which model will be first to use the process but the obvious gap in its electric SUV line-up is the EX60. That model is set to replace the hybrid XC60. The medium electric should arrive next year (or early 2026) and will probably have a 100kWh battery pack (for 600km of range). It will utilise the EX90’s electric platform and the battery pack will likely form part of the vehicle floor. This means extra structural rigidity and improved driving characteristics. Expect Thor’s-hammer LED headlight and flush door handles. It will be a rival for Audi Q6 e-tron, Porsche Macan Electric, iX3 and Tesla Model Y.
Mega-casting involves the production of large single car parts formed by pouring liquid metal into a die-cast mould. Think die-cast toys on a much larger scale. It avoids much of the welding and bolting that current techniques use. Tesla was first to use the process, then NIO and XPeng, while Toyota is introducing it soon.
Initially Volvo will create the rear floor section of its next-generation models as a single aluminium section, replacing around 100 parts used previously. It will have fewer welded joints, weigh significantly less and have similar safety and durability features to the existing item. Luggage capacity is expected to increase. The item is fully recyclable at end of life.
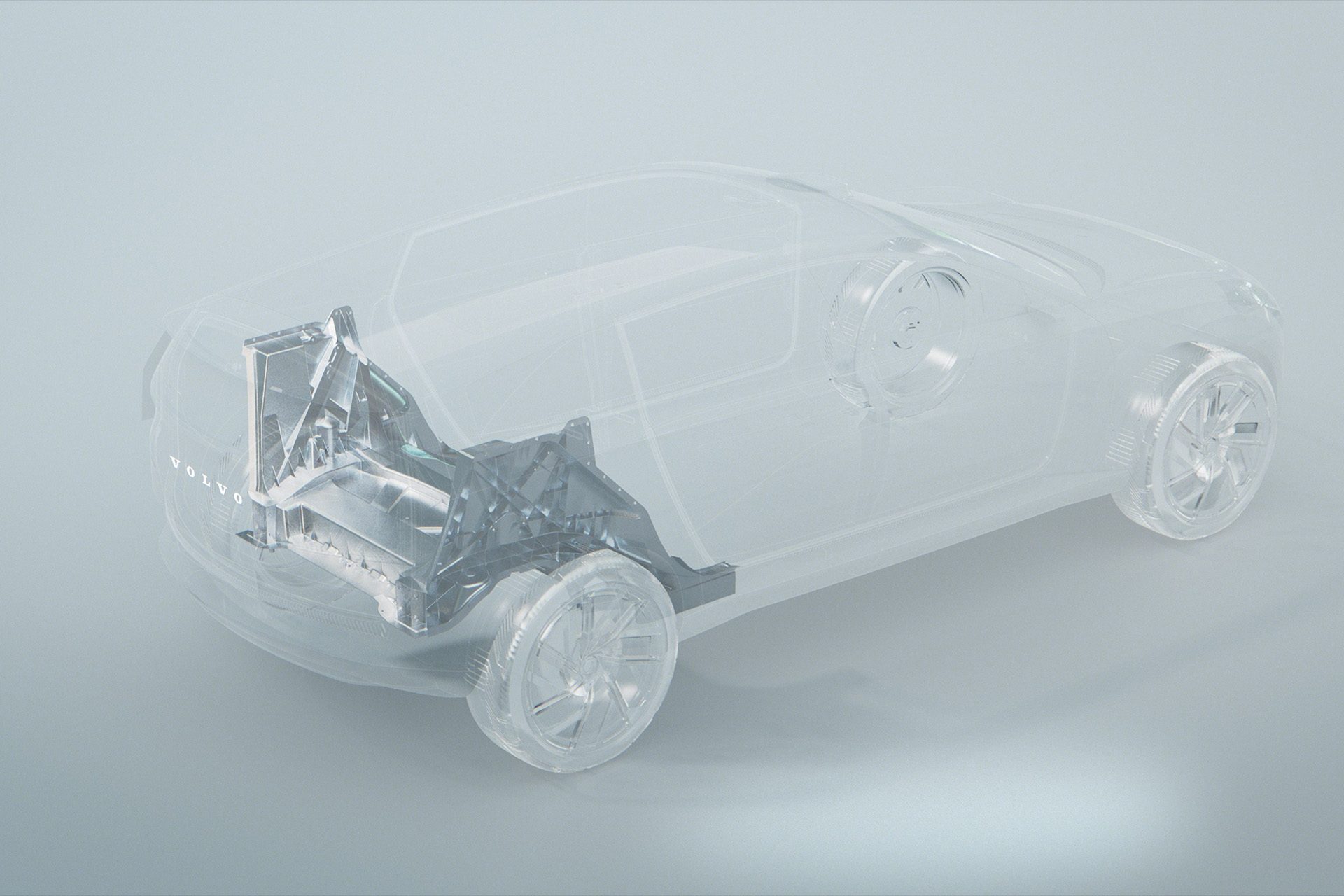
Volvo’s vehicle platform architect believes the process will revolutionise the firm’s approach to manufacturing. Current platforms have a shelf life but with megacasting you simply change the moulds. Therefore, it is much easier to make substantial changes to the physical structure. A Volvo spokesperson said any megacast platform has “an unlimited lifespan”. It will also speed up the development of new vehicle types.
The ultimate goal is to produce much of the platform as a handful of pieces. The rear floor is a sensible place to start the process because it is easy to design a rigid floor. Volvo says it has investigated mega-casting a complete battery tray because once again it replaces many parts.
There are evidently no issues with safety either. The mega-castings finish behind the wheelhouse. There is then a bumper beam and a rear crash structure which is easy to replace.
Other production benefits of mega-casting include speed of operation, major reductions in CO2 emissions and significantly higher material utilisation. Any leftover aluminium is melted down and re-used. It takes about two minutes to make a single rear tray versus an hour for a regular item. Repair of a mega-cast part is possible but unlikely.
Volvo will initially use new pressed aluminium for mega-casting but it is evaluating the use of recycled metal in the future.
The Swede is preparing its Torslanda plant for EV construction and is also opening a battery assembly plant. It will construct packs using cells produced by partner firm Northvolt. Volvo also plans to use mega-casting at a new factory being built in Slovakia.
The EX60 is expected to be unveiled later this year.